foliexperten
New Member
Last days i had a job to mount some reflective vinyl on the car. It was first time to deal with reflective vinyl so i search for some information and i made a blog with some info to help some other people.
Reflective, not Electric
Reflective vinyl is not self luminescent. Its properties aren’t apparent in normal daylight conditions. It’s specifically designed to be visible at night when stricken with artificial light such as that from motor vehicle headlights. This reflective property is what makes road signs legible after dark without the cost of electric illumination. Because of this, there is sometimes a color shift that occurs when viewing reflective vinyl in different settings.
White reflective for instance, is only white when it’s doing its thing. In normal daylight settings, it tends to look slightly grayish or pearlescent At the other end of the spectrum, black reflective has to look different when light hits it because black is the absence of light. So black reflective looks brownish when it reflects light after dark.
Retroreflective & Prismatic
Not all reflective vinyl is the same. There are two basic kinds, usually characterized as retroreflecitve, and prismatic. These are further segmented into different Types and grades determined by their construction and reflective properties, which we’ll examine in a moment. Retroreflective is made by mixing glass beads in the pigment of the face film. The embedded beads reflect light back toward the viewer when illuminated. Therefore retroreflective film is also referred to as beaded reflective.
These embedded beads make retroreflective sheeting more difficult to cut than standard PVC vinyls. Always use a 60° blade when cutting retroreflective sheeting. You can make it work with a 45° blade and lots of force, but that blade will be worthless when you’re done.
Prismatic reflective film is made by layering small prisms in the face film. Upon close inspection these would look like tiny pyramids in the vinyl. Just as a prism splits and reflects light, prismatic reflective film reflects light back through the face film toward the viewer.
This densely layered construction makes prismatic reflective sheeting even more difficult to cut than retroreflective film. Some brands such as 3M Diamond Grade, can only be cut with a Pro Series cutter using special blades and well over 400 grams of force. Other brands like Nikkalite’s Crystal Grade reflective cannot be cut with anything less than a flatbed cutter. It can be scored with a Pro Series plotter, but the cutting must then be finished by hand.
The advantage of prismatic film is that the sides of the prismatic cells in the face film bounce light back at wider angles. This results in much more light being reflected back toward the source and makes the light visible from a wider viewing angle. This is especially useful in highway signs, which is why prismatic sheeting is the specification for this application.
Once you’ve identified the category of reflective sheeting you need, there is one more critical choice to make. This one’s a little more difficult because there isn’t a consensus. Different manufacturers use varying labels called ‘grades’ to promote the quality of their reflective vinyls. ORACAL offers its ORALITE films in commercial grade and engineer grade. Avery offers “utility”, engineer, and super engineer grade. EnduraLITE is available in engineer, flexible engineer and super engineer grades. How do you choose the right product?
To simplify the choice, don’t pay too much attention to the ‘grade’ label applied to the film. Look instead at outdoor durability rating and flexibility. The outdoor rating is easy as most films tell you what to expect. They generally range from three to seven years outdoors, although the newer Type II “super engineer” grade reflectives are now rated at ten to 12 years.
Curves & Conformability
That leaves conformability as the last critical factor. This is important because reflective vinyl is not made from the same PVC compounds used in calendared and cast films. It’s made from translucent acrylic resins designed to allow the light to pass to and from the enclosed beads or prisms. This face film can be rather brittle and some films that are seven year engineer grade products will not work on anything but flat surfaces. They’re great for street signs, not so great for police and emergency vehicles. This usually causes problems when someone chooses a non-conformable reflective for fleet applications. The film sticks for a while, then begins to release from the curved surfaces. Having your newly applied graphic fall off the Sheriff’s cruiser can be bad for your career. So make sure you check that spec.
Application Tips & Digital Printing
Now that you know how to choose the right reflective product for your needs, we need to talk about application and printing. The most common error in applying reflective vinyl is the use of application fluid. This is a big no-no. The adhesives used in these products do not stand up well when applied wet. The use of any application fluid, whether it’s dish detergent or RapidTac will probably cause the vinyl to fail. Always apply reflective films dry.
As digital printers become the engine of choice for sign making, we get questions about whether reflective vinyl can be imprinted. The answer is a qualified yes. If you’re using an old fashioned thermal resin printer, you can print on most reflective vinyls, although some of them may not hold the resin as well as others. If you’re using a solvent or ecosolvent inkjet, you can print on some reflective vinyl, but not all of it. Our EnduraLITE 8100 is a popular choice for ValueJet and PrismJET VJ users. ORALITE 5300 and 5600 are also solvent printable, but 5700 is not.
For best results, we recommend EnduraLITE M8512, a 6.4 mil Type 1 retroreflective film developed specifically for use with solvent and eco-solvent inkjet printers. EnduraLITE M8512 is a conformable, seven year film meeting ASTM D4956 and E-810 standards for visibility and reflectivity. For printing on a PrismJET VJ48 or MUTOH ValueJet, use an ICC profile for glossy vinyl and set the platen and pre-heaters to 40° and 45° respectively and set the drying temperature at 50°C.

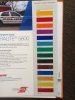
Reflective, not Electric
Reflective vinyl is not self luminescent. Its properties aren’t apparent in normal daylight conditions. It’s specifically designed to be visible at night when stricken with artificial light such as that from motor vehicle headlights. This reflective property is what makes road signs legible after dark without the cost of electric illumination. Because of this, there is sometimes a color shift that occurs when viewing reflective vinyl in different settings.
White reflective for instance, is only white when it’s doing its thing. In normal daylight settings, it tends to look slightly grayish or pearlescent At the other end of the spectrum, black reflective has to look different when light hits it because black is the absence of light. So black reflective looks brownish when it reflects light after dark.
Retroreflective & Prismatic
Not all reflective vinyl is the same. There are two basic kinds, usually characterized as retroreflecitve, and prismatic. These are further segmented into different Types and grades determined by their construction and reflective properties, which we’ll examine in a moment. Retroreflective is made by mixing glass beads in the pigment of the face film. The embedded beads reflect light back toward the viewer when illuminated. Therefore retroreflective film is also referred to as beaded reflective.
These embedded beads make retroreflective sheeting more difficult to cut than standard PVC vinyls. Always use a 60° blade when cutting retroreflective sheeting. You can make it work with a 45° blade and lots of force, but that blade will be worthless when you’re done.
Prismatic reflective film is made by layering small prisms in the face film. Upon close inspection these would look like tiny pyramids in the vinyl. Just as a prism splits and reflects light, prismatic reflective film reflects light back through the face film toward the viewer.
This densely layered construction makes prismatic reflective sheeting even more difficult to cut than retroreflective film. Some brands such as 3M Diamond Grade, can only be cut with a Pro Series cutter using special blades and well over 400 grams of force. Other brands like Nikkalite’s Crystal Grade reflective cannot be cut with anything less than a flatbed cutter. It can be scored with a Pro Series plotter, but the cutting must then be finished by hand.
The advantage of prismatic film is that the sides of the prismatic cells in the face film bounce light back at wider angles. This results in much more light being reflected back toward the source and makes the light visible from a wider viewing angle. This is especially useful in highway signs, which is why prismatic sheeting is the specification for this application.
Once you’ve identified the category of reflective sheeting you need, there is one more critical choice to make. This one’s a little more difficult because there isn’t a consensus. Different manufacturers use varying labels called ‘grades’ to promote the quality of their reflective vinyls. ORACAL offers its ORALITE films in commercial grade and engineer grade. Avery offers “utility”, engineer, and super engineer grade. EnduraLITE is available in engineer, flexible engineer and super engineer grades. How do you choose the right product?
To simplify the choice, don’t pay too much attention to the ‘grade’ label applied to the film. Look instead at outdoor durability rating and flexibility. The outdoor rating is easy as most films tell you what to expect. They generally range from three to seven years outdoors, although the newer Type II “super engineer” grade reflectives are now rated at ten to 12 years.
Curves & Conformability
That leaves conformability as the last critical factor. This is important because reflective vinyl is not made from the same PVC compounds used in calendared and cast films. It’s made from translucent acrylic resins designed to allow the light to pass to and from the enclosed beads or prisms. This face film can be rather brittle and some films that are seven year engineer grade products will not work on anything but flat surfaces. They’re great for street signs, not so great for police and emergency vehicles. This usually causes problems when someone chooses a non-conformable reflective for fleet applications. The film sticks for a while, then begins to release from the curved surfaces. Having your newly applied graphic fall off the Sheriff’s cruiser can be bad for your career. So make sure you check that spec.
Application Tips & Digital Printing
Now that you know how to choose the right reflective product for your needs, we need to talk about application and printing. The most common error in applying reflective vinyl is the use of application fluid. This is a big no-no. The adhesives used in these products do not stand up well when applied wet. The use of any application fluid, whether it’s dish detergent or RapidTac will probably cause the vinyl to fail. Always apply reflective films dry.
As digital printers become the engine of choice for sign making, we get questions about whether reflective vinyl can be imprinted. The answer is a qualified yes. If you’re using an old fashioned thermal resin printer, you can print on most reflective vinyls, although some of them may not hold the resin as well as others. If you’re using a solvent or ecosolvent inkjet, you can print on some reflective vinyl, but not all of it. Our EnduraLITE 8100 is a popular choice for ValueJet and PrismJET VJ users. ORALITE 5300 and 5600 are also solvent printable, but 5700 is not.
For best results, we recommend EnduraLITE M8512, a 6.4 mil Type 1 retroreflective film developed specifically for use with solvent and eco-solvent inkjet printers. EnduraLITE M8512 is a conformable, seven year film meeting ASTM D4956 and E-810 standards for visibility and reflectivity. For printing on a PrismJET VJ48 or MUTOH ValueJet, use an ICC profile for glossy vinyl and set the platen and pre-heaters to 40° and 45° respectively and set the drying temperature at 50°C.