Ill put up a better picture of it on the wall in use. Hope it helps with some ideas. We do heavy equipment, industrial painting and body work on trucks equipment etc so our board isnt exactly relevent to a sign shop. The board is left to right work flow, incoming jobs go on the left (we have job magnets with permanent job numbers that we use a dry erase on) new go On the "cold" part of the arrow and get moved up to the top. The larger boxes are stages in process, theres a check box when a stage is complete and a foreman checks it before moving it to the next stage. The smaller boxes are where the jobs are waiting to go. Color coded by process. My reasoning for color coding is that i dont want any job process jumping around, i.e. If its in blast it can only move to prime body or sanding, it cant go back to get cleaned more. More of a visual for employees that each stage has to be 100% before advancing like a board game kind of. We have white magnets for normal jobs, red for rush jobs and blue for a regular contract we have that demands priority scheduling. We have/had problems with doing 90% of say body work, putting it our paint booth then doing another days worth of body work in the booth. Or intial cleaning is "finished" then when its critical time wise to move to paint, were cleaning grease off while were taping, pushing paint back a day, tieing up our booth and pushing the entire schedule back a day. I dont know if what i said makes any sense? We also have job sleeves with details that coorespond with the magnet in a holder next to the board. Google 5s production board or lean management board etc for more ideas. I like this stuff so if you wanted a clarification on what we did let me know. We also are in the process of eliminating all flat areas, shelves etc in our shop to go along with it. Ill get some better pics in a few days
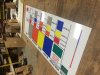