jetgraphicsmi
New Member
I know there have been a few discussions on this topic here, but I wanted to get a fresh perspective. I just finished a sprinter van for a customer, and I'm not very happy with the way it turned out. The graphic was a partial wrap, with the logo spanning a few of the deep channels in the side of the van and a large swoosh design over the back end also covering some of the channels (see image). The van was painted at some point in it's life. It was white, but it was clearly painted black. The customer also used a stripping wheel to remove some existing graphics.
To prep the surface, I sprayed with water/dish soap combo and wiped it down to remove surface dirt. I then used Rapid Prep to clean the entire surface again. Then again with Rapid Tac II. I also cleaned the deep channels out with 70% Isopropyl Alcohol.
I used Oracal 3951 RA with Oracal 290 G laminate. I applied the graphics flat to the sides, then used a heat gun to heat and press the vinyl into the channels. I pressed in with both soft and hard squeegees and I wear gloves when installing. Once the vinyl cooled and it was laid in place with no bubbles. I hit it with the heat again. My shop is kept at between 65 and 70 degrees F. Almost immediately the vinyl bubbled and pulled away from the deep channels. Unfortunately, no amount of heat or pressing would get it to stay put, so in the end, I had no choice but to make relief cuts. It solved the problem, but it obviously is not a clean look. The customer was happy with the final outcome, and the truck looks good, but I'm a perfectionist and I want my wraps to be as seamless as possible.
I chose Oracal because it states in their literature that 3951 is designed for this type of application. Of course now I'm reading about primers and "laying" in the vinyl, which is not always possible. I'm also reading good things about 3M ij380. I'm a little frustrated that I may have a wrap coming back to me soon for re-work. Any thoughts or suggestions would be greatly appreciated. Thank you.
Jason
PS. We let each print off gas for 24 hours before laminating.
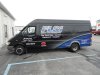
To prep the surface, I sprayed with water/dish soap combo and wiped it down to remove surface dirt. I then used Rapid Prep to clean the entire surface again. Then again with Rapid Tac II. I also cleaned the deep channels out with 70% Isopropyl Alcohol.
I used Oracal 3951 RA with Oracal 290 G laminate. I applied the graphics flat to the sides, then used a heat gun to heat and press the vinyl into the channels. I pressed in with both soft and hard squeegees and I wear gloves when installing. Once the vinyl cooled and it was laid in place with no bubbles. I hit it with the heat again. My shop is kept at between 65 and 70 degrees F. Almost immediately the vinyl bubbled and pulled away from the deep channels. Unfortunately, no amount of heat or pressing would get it to stay put, so in the end, I had no choice but to make relief cuts. It solved the problem, but it obviously is not a clean look. The customer was happy with the final outcome, and the truck looks good, but I'm a perfectionist and I want my wraps to be as seamless as possible.
I chose Oracal because it states in their literature that 3951 is designed for this type of application. Of course now I'm reading about primers and "laying" in the vinyl, which is not always possible. I'm also reading good things about 3M ij380. I'm a little frustrated that I may have a wrap coming back to me soon for re-work. Any thoughts or suggestions would be greatly appreciated. Thank you.
Jason
PS. We let each print off gas for 24 hours before laminating.
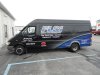
Last edited: